Steel CNC Machining – CNC Machining Steel Services and Parts Supplier
CNCJY manufacturing delivers a new screw machined custom component more than one million times a month, including hundreds of thousands of steel parts. The production of each component is focused on high productivity and on ensuring a constant supply of components. Hundreds of different steel alloy types, each with specific processing requirements that we have mastered over the course of the last half-century, back up this assurance.
Why Should I Choose CNCJY for Steel CNC Machining Services and Parts
-An Esprit CAD/CAM system coupled with CNCJY’s high-precision machinery ensures that the most complex geometries can be manufactured to exacting specifications.
-Making your own tools allows you to better match the steel you’re working with when designing your tools.
-Skilled machining craftsmen are adept at spotting potential problems before they enter a production run.
Why Mild Steel CNC Machining Services are Popular?
For many general engineering applications, mild steel is one of the most widely available materials with unrivaled properties. Mild steel CNC machining has become increasingly popular and widely used due to the following characteristics.
-Mild steel is flexible; hence can be machined and shaped easily.
-As opposed to higher carbon steel, mild steel is easy to shape, drill, weld, and cut to required specifications.
-It has good resistance against breakage.
-Mild steel possesses good impact resistance.
-The steel is compatible with several finishing operations.
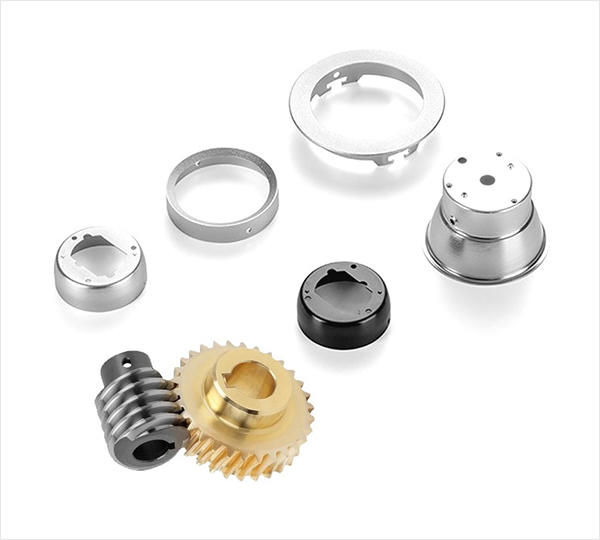
Common Alloys and Specifications of CNC Machining Steel
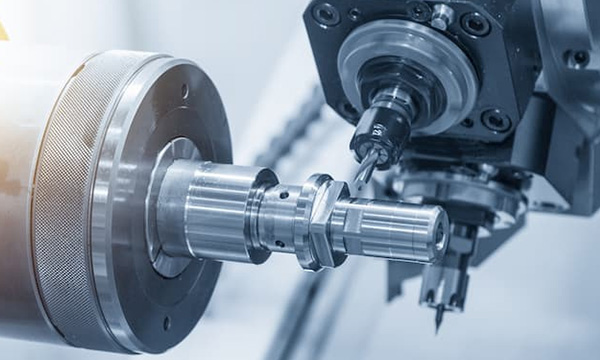
Steel and aluminum are popular materials in industries that require high-performance, long-lasting parts, such as the automotive, aerospace, and robotics industries. However, steel and aluminum have very different physical properties and price points, so it’s critical to know which is best for a given part. One of these determining factors is the manufacturing method, which is frequently CNC machining in these industries. There are several key reasons why steel may be a better material choice than aluminum when machining a metal part. While aluminum is extremely light, steel is significantly stronger. Furthermore, aluminum is much more expensive.
However, the choice is not simply between aluminum and steel. Steel is a material family, and it is critical to carefully evaluate different steels – and their respective benefits and limitations – during the material selection process. Here are the four most commonly machined steel types, as well as what product teams should know about each.
1.4140 Steel
Because of its high fatigue strength, overall toughness, and resistance to abrasion and impact, 4140 steel is used in a variety of industries. Because 4140 steel is much tougher than plain carbon steel, it requires more force to form effectively. Furthermore, annealing is more important when machining 4140 steel than when machining simple, low-carbon steel. While it is frequently quench-hardened, 4140 is difficult to weld and will require pre- and post-weld thermal treatment to prevent cracking, as well as the use of compatible filler material. 4140 requires slightly more material than non-alloy, pure carbon steel, as well as significantly more machining. However, because it is so strong and durable, it is thought to be very cost-effective.
Mechanical specifications:
Heat treatment | Ultimate Tensile Strength | Elongation at Break | Modulus of Elasticity | Hardness |
---|---|---|---|---|
Oil quenched, 540°C temper, 25mm round | 1140 MPa | 18% | 205 GPa | 35 HRC |
2.1018 Steel
Although 1018 steel is very weldable, it is not as hard as some other steels. The main advantage of 1018 steel is its workability. It is very simple to form, forge, weld, and hot work, making it ideal for parts requiring severe bends or other fine features. As a result, 1018 steel is frequently used for shafts, spindles, pins, and rods. It’s also a good option for carburized parts. The machinability, strength, and precision of 1018 steel come at a high cost. It is more expensive than some comparable steels, but it is far better suited for CNC machining.
Mechanical specifications:
Heat treatment | Ultimate Tensile Strength | Elongation at Break | Modulus of Elasticity | Hardness |
---|---|---|---|---|
Cold-drawn | 440 MPa | 15% | 200 GPa | 71 HRB |
3.1045 Steel
1045 Steel is a high-strength, high-hardness medium carbon steel. Its size precision, straightness, and concentricity make it ideal for high-speed applications. It is frequently used in the manufacture of bolts, studs, gears, axles, and shafts. Because 1045 is a medium-tensile strength steel with medium hardenability, it is not suitable for applications requiring a very high-strength material. 1045 steel is more expensive and has higher strength than 1018 steel, but it has similar weldability and machinability, which contributes to its higher cost.
Mechanical specifications:
Heat treatment | Ultimate Tensile Strength | Elongation at Break | Modulus of Elasticity | Hardness |
---|---|---|---|---|
Cold-drawn | 625 MPa | 12% | 206 GPa | 88 HRB |
4.4130 Steel
4130 steel has a higher modulus of elasticity than most other steels of comparable ultimate strength, allowing it to withstand high stresses. 4130 is commonly used in the manufacturing of machinery, rock crushing machinery, and resistance welding products. 4130 steel is suitable for a wide range of heat treatment processes. 4130 steel is low-cost steel in terms of both raw material and cutting costs. It has physical properties that are similar to aircraft-grade stainless steel, but at a much lower cost, making it a desirable option for many product teams.
Mechanical specifications:
Heat treatment | Ultimate Tensile Strength | Elongation at Break | Modulus of Elasticity | Hardness |
---|---|---|---|---|
Water-quenched 855°C, 450°C temper, 25mm round | 993 MPa | 18.5% | 205 GPa | 31 HRB |
CNC Machining Steel Parts Compared – What Type of Steel is Best for Your CNC Machining Part
Alloy | eneral Characteristics | Common Applications | Tolerances for a 1/2″ Dia. Bar | Material Cost Factor | Machining Cost Factor |
---|---|---|---|---|---|
1008 | Moderate strength and low-stress applications, | Rivets and parts requiring strong welds | + .002 | 1.2 | 3.5 |
1018 | The machinability of this low carbon steel is poor, but it can be formed and welded well. | Rivets and parts requiring strong welds | Cold drawn 0 | 0.9 | 2.4 |
1045 | Strength, impact resistance and higher tensile strength. | Responds to heat treatment extremely well, but it not recommended for case hardening | + .003 | 0.9 | 3 |
1137 | Higher carbon, higher strength, direct hardening | Higher stress applications, gears, shafts, studs, etc. | Cold drawn0 | 1.6 | 2.7 |
11L37 | Strength and machinability | Easily machined and can be annealed, quenched, tempered, and heat treated | +0.03 | 5.1 | 2.2 |
11L41 | Strength and hardness and a more uniform surface hardness | Axles, shafts, bolts, and pins | +0.03 | 2.5 | 2.3 |
12L14 | Designed for excellent machinability. Case hard only | Endless commercial products, probably more pounds used it turned products than any other bar stock | Cold drawn 0 | 1 | 1 |
1215 | Designed for good machinability. Case harden only | Parts needing better formability or weldability than 12L14 | Cold drawn 0 | 1 | 1.2 |
4130 | Strength, toughness, and fatigue resistance | Military and commercial aircraft parts | Norm AQ HT Condition F4 | 1.52 | 2.7 |
4140 or 4142 | Popular general-purpose alloy. Direct hardening | Gears, shafts, pins, bolts and nuts, pump and valve components | Cold drawn 0 | 1.1 | 2.9 |
41L40 | Designed for better machining w/lead additive, direct hardening | Couplings, shafts, tooling, bolts | Cold drawn 0 | 2.5 | 2.8 |
8620 | .55% Ni, .50% Cr, .20% Mo, heat treatable and case hardening | Shafts, bushings, pins, gears, bolts | Cold drawn 0 | 2.5 | 2.9 |
52100 | Very high 1% carbon, .25% Ni, 1.4% Cr, .0.8 Mo | Bearing applications | Cold drawn Spheroidize annealed+/- .00 | 1.8 | 4.8 |