CNCJY PPS Service
PPS is well suited for corrosive structural applications or as a lower-temperature replacement for PEEK. Its low ionic impurities make it an excellent choice for applications requiring high purity. Additional PPS grades, such as glass filled, glass/mineral filled, and internally lubricated, are available, as are formulations within these grades that offer low friction, high limiting PVs, bearing strength, wear resistance, heat stability, increased impact strength, and static control properties to meet a variety of requirement levels. Contact a CNCJY representative for assistance in selecting the best material for your application.
About Polyphenylene Sulfide (PPS)
Polyphenylene sulfide (PPS) is a semi-crystalline engineering thermoplastic with a high melting point. It is an opaque, rigid polymer with a high melting point (280°C). In terms of properties, it can compete with PTFE, PEEK, and even PI (Polyimide). It is priced somewhere between PTFE and PEEK, making it a good compromise between the two. It is also easily processed, and its toughness increases at high temperatures. Polyphenylene sulfide is a preferred alternative to metals and thermosets for use in automotive parts, appliances, electronics, and a variety of other applications due to these advantages.
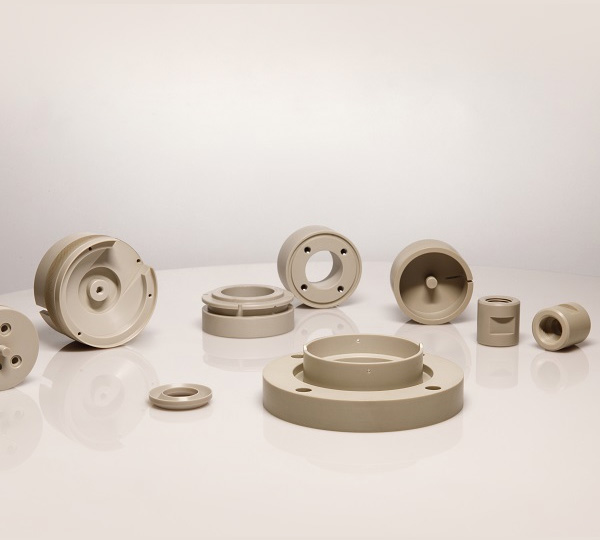
Properties of Polyphenylene Sulfide (PPS)
Crystal Structure and Physical Properties
PPS is a polymer that is semi-crystalline. Understanding the recommended processing parameters requires knowledge of the crystallization behavior of PPS. The phase transition temperatures of PPS are shown in the table below. Ranges are determined by mol. weight and curing status (linear or crosslinked).
Glass Transition Temperature (Tg) | 85-95°C |
Crystallization on Heating (Tc-h) | 120-140°C |
Cristallite Melting (Tm) | 275-285°C |
Recrystallization on cooling(Tc-c) | 255-225°C |
Density | 1.35g/cm3 |
Gamma Radiation Resistance | Good |
UV Light Resistance | Good |
HDT @0.46 Mpa (67 psi) | 140-160°C |
HDT @1.8 Mpa (264 psi) | 100-135°C |
Max Continuous Service Temperature | 200-220°C |
Thermal Insulation (Thermal Conductivity) | 0.29-0.32 W/m.k |
Dimensional Stability
PPS is an excellent material for producing complex parts with extremely tight tolerances. Even when exposed to high temperatures and humidity, the polymer maintains excellent dimensional stability.
Coefficient of Linear Thermal Expansion | Shrinkage | Water Absorption |
---|---|---|
3-5 x 10-5 /°C | 0.6-1.4% | 0.01-0.07% |
Electrical Properties
PPS is extremely electrically insulating. After exposure to high-humidity environments, both the high-volume resistivity and the insulation resistance are retained. It has a lower O2 sensitivity and can be easily doped to achieve high conductivity.
Arc Resistance | Dielectric Constant | Dielectric Strength | Dissipation Factor | Volume Resistivity |
---|---|---|---|---|
124 sec | 3-3.3 | 11-24 kV/mm | 4-30 x 10-4 | 15-16 x1015 Ohm.cm |
Thermal Properties and Fire Resistance
PPS is a specialty polymer that can withstand high temperatures. The majority of PPS compounds meet the UL94V-0 standard without the addition of a flame retardant. PPS is resistant to 260°C for a short period of time and can be used below 200°C for an extended period of time.
Fire Resistance (LOI) | Flammability UL94 |
---|---|
43-47% | V0 |
Mechanical Properties
PPS has high strength, rigidity, and low degradation properties even at high temperatures. It also has a high fatigue resistance and creep resistance.
Elongation at Break | 1-4% |
Elongation at Yield | 1-4% |
Flexibility(Flexural Modulus) | 3.8 – 4.2 Gpa |
Hardness Rockwell M | 70-85 |
Hardness Shore D | 90-95 |
Stiffness (Flexural Modulus) | 3.8-4.2 Gpa |
Strength at Break (Tensile) | 50-80 Mpa |
Toughness (Notched Izod Impact at Room Temperature) | 5-25 J/m |
Strength at Yield (Tensile) | 50-80 Mpa |
Young Modulus | 3.3-4 Gpa |
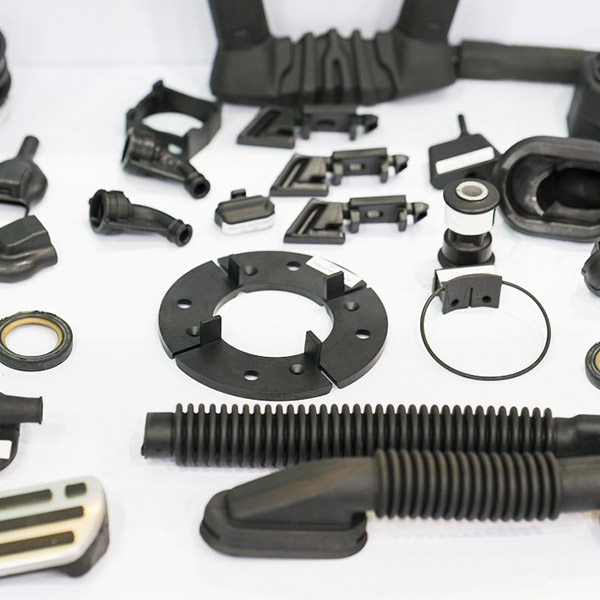
Why applications of PPS are so popular
PPS’s excellent properties, combined with its ease of production and low cost, make it one of the best choices for a variety of applications where low cost and high performance are critical.
– Automobile Applications and Parts
Polyphenylene Sulfide applications in the automotive market have grown rapidly, owing primarily to its ability to replace metal, thermosets, and other types of plastic in higher-demand applications. It is an excellent choice for automotive parts that have been exposed to:
- High temperatures
- Vehicle fluids
- Mechanical stress
PPS is a lighter-weight alternative to metals that is resistant to salt corrosion and all automotive fluids. The ability to mould complex parts to tight tolerances, as well as insert moulding, allows for multiple component integrations. The largest application area for PPS is in the engine compartment, followed by electrical parts. Fuel injection systems, coolant systems, water pump impellers, thermostat holders, electric brakes, switches, bulb housing, and other automotive applications use PPS. It is almost never used to make interior or exterior auto parts.
Applications in Electronics and Electrical Engineering
PPS is a material of choice in the E&E industry because of its high temperature resistance, high toughness, good dimensional stability, and good rigidity.
- Allows for precise molding of connectors and sockets with excellent flow and low shrinkage.
- Offers increased structural rigidity and mechanical integrity for dependable construction
- Is the most reliable option for soldering.
In addition, flame-retardant-free PPS compounds can achieve UL94 V-0 ratings. To accommodate the requirements of high precision moulding, specialized low flash grades have been created. Polyphenylene sulfide is also used in the production of numerous electrical and electronic components, such as bobbins and connectors, hard disk drives, electronic housings, sockets, switches, and relays. Substituting other, lower-temperature polymers for PPS in electrical/electronic applications is a major factor limiting its growth.
– Appliances
PPS can be used to manufacture heating and air conditioning components, fry pan handles, hair dryer grills, Steam iron valves, toaster and dryer switches, microwave oven turntables, etc. in electric appliances because of its exceptional dimensional stability, low density, corrosion and hydrolysis resistance.
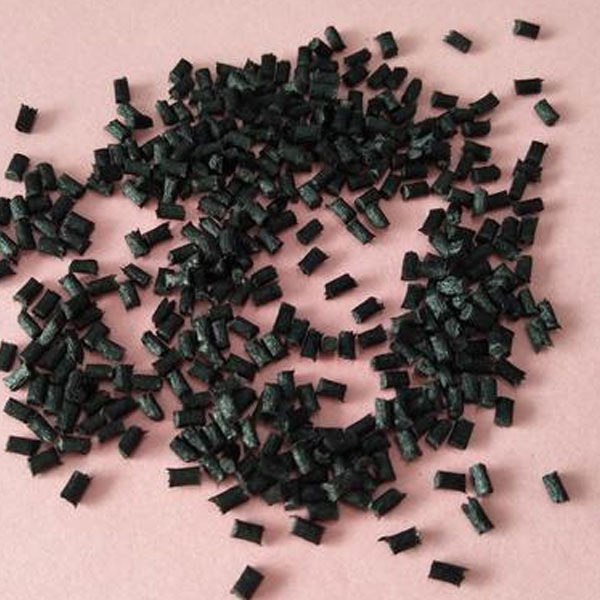
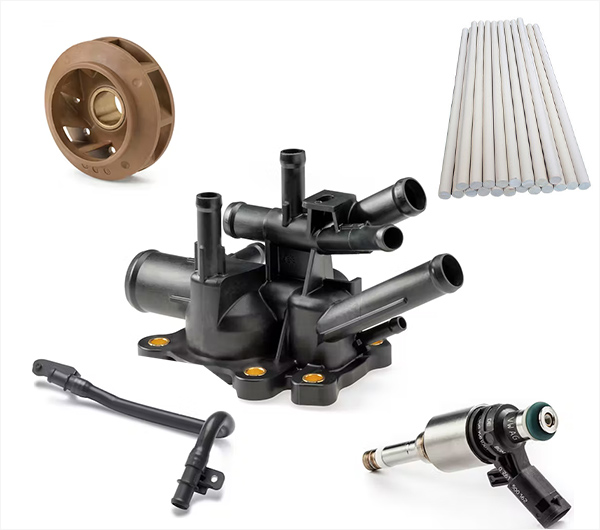
– Industrial Applications
In mechanical engineering, PPS has replaced metal alloys, thermosets, and many other thermoplastics. Polyphenylene Sulfide’s thermal stability and broad chemical resistance make it ideal for use in extremely hostile chemical environments.
- It is useful in a wide range of heavy industrial settings, including those unrelated to reinforced injection moulding compounds.
- Fiber extrusion and non-stick and chemical-resistant coatings are some of the applications for this material.
- Suitable for mechanically and thermally high-stressed moulded components.
- Pumps, valves, and piping are among the many machine-building and precision engineering components to which PPS is applied.
- Besides oil field equipment, it can also be found in components such as lift and centrifugal pump parts as well as oil patch drop balls, rod guides and scrapers
- It is used in the heating, ventilation, and air conditioning (HVAC) sector for compressors, mufflers and storage tanks, hot water circulation components, induced draft blower housing and power vent components.